Back in the old days, the seventies and eighties, it was up to us pilots to push the engine to its limits and to make sure its limits were not exceeded. After every flight where the engine held together, we thought we had done it again. But after engine failure after engine failure it became obvious we were either exceeding the limits and not telling any one, pushing the limits repeatedly was causing cumulative damage, or both.
— James Albright
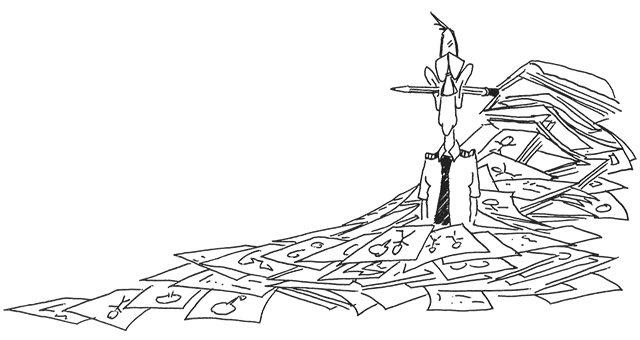
Updated:
2012-05-04
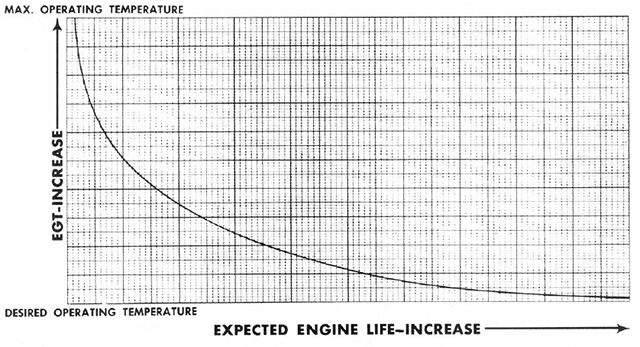
Expected Engine Life, from 1C-135(E)C-1, Figure 7-3A.
Understanding the liquid nature of metals will help you prolong the life of your very expensive engines. Most of which follows comes from my Air Force Boeing 707 manual. I will agree that engines these days are made better, last longer, fail less often, and have lots of computers to keep you out of trouble. I also concede that the chart above and the technical details below may not remotely reflect the engines strapped to your airplane. But all of this is an excellent primer on possible failure modes for your jet engine.
Our Boeing 707 squadron went through a few years where we lost an engine a month. With four aircraft, each with four engines, the odds were not good. Here's what we learned from all that: just because you are operating the engine within its published limits doesn't mean you are taking good care of it.
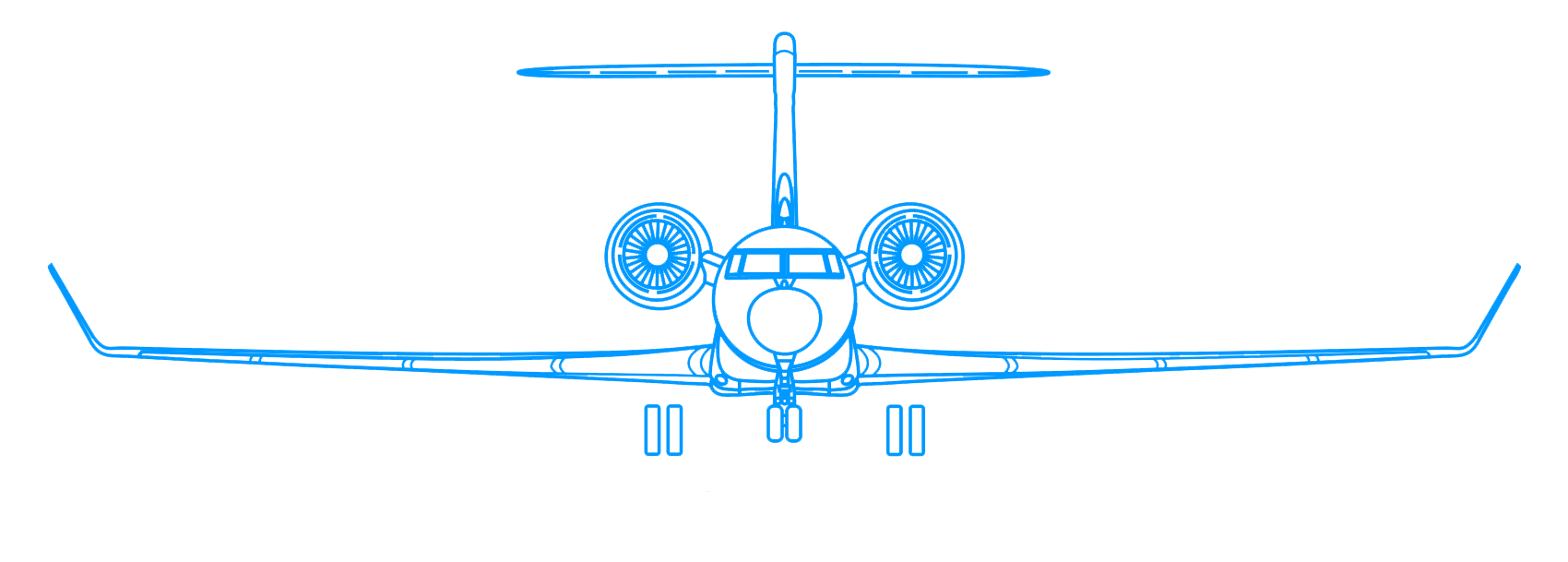
1
Starting to Understand the Problem
In the early eighties, the Air Force started adding "Engine Creep" paragraphs to flight manuals. These paragraphs remain the best thing I've ever seen on the subject, despite a few flaws in logic.
- The "Time-temperature-rpm" relationship within the engine is the main factor in engine life. The most important of these is temperature. The strengths of the materials used in the engine decrease as high internal temperatures approach the melting points of the metals, even though the danger point may not be closely approached. There is a tendency for any material to take a permanent set, stretch or bend; this tendency increases with both the load and the temperature. The amount of permanent set increases with the length of time that the load and/or temperature is applied. After a certain amount of permanent set is attained, the fibers or grains of the material begin to pull apart. Under inspection with a high powered microscope, the beginnings of fine cracks may be seen. With additional time, the material begins to elongate at faster rates as the cracks become bigger and deeper. Finally, the material breaks. This process is so slow that elongation is perceptible only with careful measurement. The term "creep" has been applied to the process because of the length of time required for elongation to become significant. In a turbine engine, high load and high temperature are usually experienced at the same time. The loading on the turbine and compressor blades is principally the combined result of centrifugal force, associated with rpm, and some gas or air load, associated with engine internal pressure. When the turbine discharge pressure, which is indicative of other internal pressures, is high, the EGT is also high. This means that when the turbine blades are subjected to their heaviest load, the material of which they are constructed will be at its weakest. The compound effect of high rpm and high temperature results in an astounding increase in the rate of creep at very high thrust settings when the centrifugal load is the greatest. The ends of the compressor blades and the rims of the turbine wheels tend to travel outward. The rate of creep, which is measured in millionths of an inch per hour, increases tremendously as the rpm and EGT approach maximum. Numbers can be assigned to the relative amounts of creep to show what actually happens at varying EGT and rpm. For a typical TF33 turbine blade, the rate of creep is approximately as follows:
- Turbine life is inversely proportional to the number of creep units per hour. The pilot controls the rate of creep by the manner in which he operates the engine. Turbine blades are carefully inspected and measured at engine overhaul. Those which are elongated beyond tolerable limits and those which show evidence of distortion or cracks must be replaced. In extreme cases, the blades may even fail before the engine comes due for overhaul. It can be readily seen from the foregoing creep rate table that when an engine is operated at the lowest temperature and rpm shown, the turbine blades will last 2500 times as long as they will if the engine is operated at the highest temperature and rpm shown. This is the reason that EGT during engine acceleration is time limited. Although the pilot cannot "read" the creep rate of turbine blades, he can "read" the operating temperature of the engine as EGT.
- A definite relationship exists between excessive EGT and premature engine removals. The fuel control normally maintains EGT within a safe margin. However, the control cannot compensate for operational malpractices. Furthermore, under extreme flight conditions or in the event of a malfunction, the regulation of engine internal temperatures can be marginal or even above desired limits. Therefore the pilot must develop a "temperature sense" by thinking in terms of the inter-relationship of the engine control factors. By so doing one can learn either to avoid excessive temperatures altogether or to take immediate action should they occur. Do not use a thrust or power setting higher than is necessary to accomplish the assigned mission.
EGT - °C | RPM (N2) | CREEP |
---|---|---|
450 | 95% | 1 unit per hour |
525 | 97% | 5 units per hour |
555 | 100% | 50 units per hour |
585 | 101% | 2500 units per hour |
Source: Technical Order 1C-135(E)C-1, pg. 7-4
2
Starting to Deal with the Problem
Every airplane I've flown since the B-707 automatically records these "excursions" over the limits and the later ones even make note of the time and date. But now, things have gone to the next level:
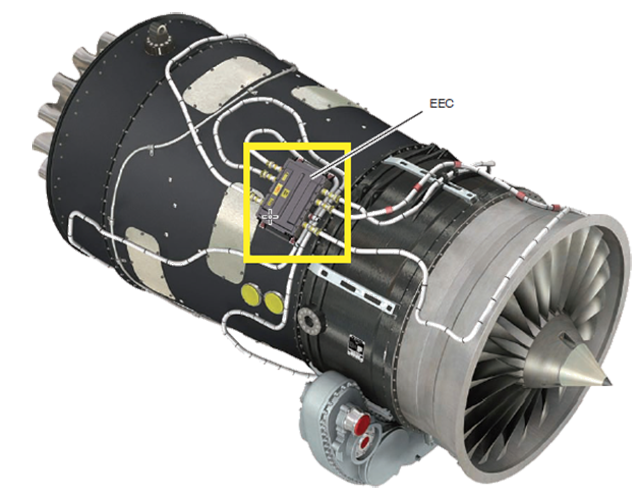
EEC Location, from FSI G450 PTM, pg. 7-22.
In the Gulfstream GV/G450/G550 world, FADEC is either "Full Authority Digital Engine Control" or "Full Authority Digital Electronic Control." Either way, the thing running the engine is not the pilot, it's this:
The EEC, the Electronic Engine Control is the part of the FADEC that interprets your power lever movements as requests and turns those into fuel and guide vane commands that gives you more or less power, but it will not allow you to damage the engine.
But what if you do? On this particular airplane, the airplane sends off an e-mail to Gulfstream, the airplane's director of maintenance and chief pilot. It will rat me out to me.
References
(Source material)
Ejaz. N., Quershi, I. N., Rizvi, S. A., Creep Failure of low pressure turbine blade of an aircraft engine, Engineering Failure Analysis 18 (2011) 1407-14.
FSI G450 PTM, FlightSafety Interaction Gulfstream G450 Pilot Training Manual, Volume 2, Aircraft Systems, October 2008
Technical Order 1C-135(E)C-1, EC-135C Flight Manual, USAF Series, 15 February 1966.
Please note: Gulfstream Aerospace Corporation has no affiliation or connection whatsoever with this website, and Gulfstream does not review, endorse, or approve any of the content included on the site. As a result, Gulfstream is not responsible or liable for your use of any materials or information obtained from this site.