Mechanics are just as likely as pilots to become complacent as they grow with experience and earn the respect of their peers. In fact, in many ways they are at greater risk. They are not subjected to the same regimen of training and evaluation; they can go longer without a "course correction" to bring them back into the standards they were initially trained to. Mechanics can often be relied upon to work alone, even in large shops, and they may find themselves inspecting their own work. In some cases, the first test of a mechanic's work is the next time the airplane flies with a load of passengers. This is a case study of just such a mechanic.
— James Albright
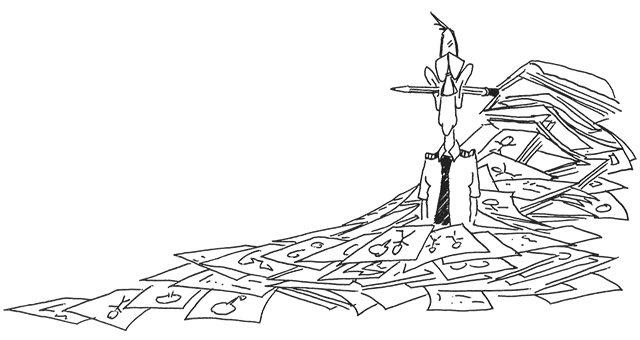
Updated:
2016-07-11
The mechanic in question exhibited all four aspects of what I call "Maintenance Malpractice." He took several short cuts, bypassed the chance for a second set of eyes to perform quality assurance, may have not been recently trained to relearn lessons he had forgotten, and he wasn't properly rested. He is very lucky nobody died.
So this is a flight mishap but we won't be discussing the flight other than to say the pilot's windshield blew out passing 17,300' because it was installed improperly. The captain was blown mostly out of the cockpit and would have died hadn't it been for the efforts of the cabin crew holding onto him and of the first officer for getting the airplane on the ground quickly. We pilots can learn from this exercise, however. Look your airplanes over carefully after maintenance. If you have a one mechanic shop, develop a rapport and volunteer to be that second set of eyes. The life this effort saves could be yours.
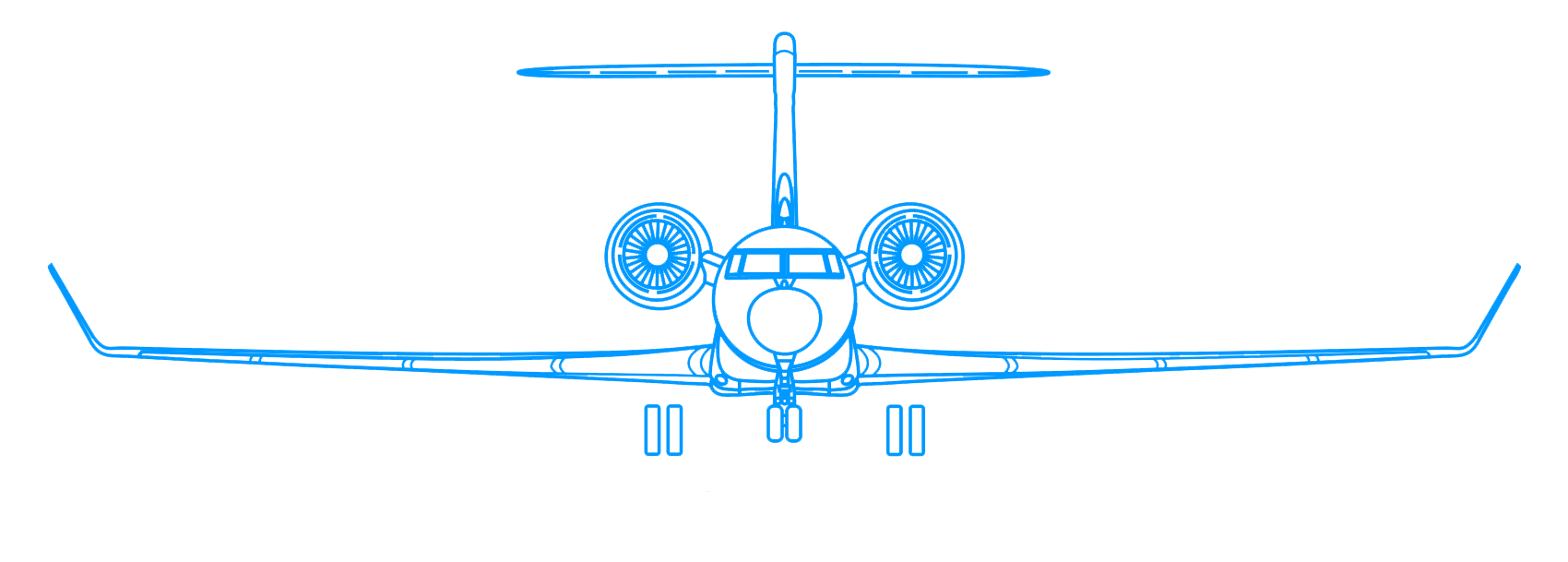
1
Accident report
- Date: 10 June 1990
- Time: 7:33
- Type: BAC One-Eleven 528FL
- Operator: British Airways
- Registration: G-BJRT
- Fatalities: 0 of 6 crew, 0 of 81 passengers
- Aircraft Fate: Repaired
- Phase: En route
- Airport: (Departure) Birmingham International Airport (BHX/EGBB), United Kingdom
- Airport: (Destination) Malaga Airport (AGP/LEMG), Spain
2
Narrative
The Flight
- The accident occurred during a scheduled flight (BA 5390) from Birmingham to Malaga, Spain. With 81 passengers, four cabin crew and two flight crew the aircraft took off from Birmingham International Airport at 0720 hrs and, having been transferred by ATC to the Daventry and then the Bristol Sector Controller of London Air Traffic Control Centre (LATCC), was cleared to Flight Level (FL) 140. A number of radar headings were ordered until the flight was instructed to maintain a radar heading of 195°M and cleared for a further climb to FL 230. The co-pilot had been the handling pilot during the take-off and, once established in the climb, the commander was handling the aircraft in accordance with the operator's normal operating procedures. At this stage both pilots had released their shoulder harness, using the release bar on the buckle, and the commander had loosened his lap-strap.
- At 0733 hrs as the cabin staff prepared to serve a meal and drinks, and, as the aircraft was climbing through about 17,300 feet pressure altitude, there was a loud bang and the fuselage filled with condensation mist. It was at once apparent to the cabin crew that an explosive decompression had occurred. The commander had been partially sucked out of his windscreen aperture and the flight deck door had been blown onto the flight deck where it lay across the radio and navigation console. The No 3 steward, who had been working on the cabin side of the door, rushed onto the flight deck and grasped the commander round his waist to hold on to him. The purser meanwhile removed the debris of the door and stowed it in the forward toilet. The other two cabin staff instructed the passengers to fasten their seat belts, reassured them and took up their emergency positions.
- The co-pilot immediately attempted to control the aircraft and, once he had regained control, initiated a rapid descent to FL11O. He re-engaged the autopilot which had become disconnected by displacement of the control column during the commander's partial egress and made a distress call on the frequency in use but he was unable to hear its acknowledgment due to the noise of rushing air on the flightdeck. There was some delay in establishing two-way communications and consequently the Bristol Sector Controller was not immediately aware of the nature of the emergency. This led indirectly to the LATCC Watch Supervisor not advising the aircraft operator of the incident, as required by the Manual of Air Traffic Services (MATS) part 1. Consequently the initiation of the British Airways Emergency Procedure Information Centre plan was delayed. Meanwhile the purser re-entered the flight deck and, having hooked his arm through the seat belts of the fourth crew member jump seat which was located behind the left-hand pilot's seat, was able to assist the No 3 steward in the restraint of the commander.
- The two men tried to pull the commander back within the aircraft and, although they could see his head and torso through the left Direct Vision (DV) window, the effect of the slipstream frustrated their efforts. The No 2 steward entered the flight deck and he was able to relieve the No 3 steward whose arms were losing their strength as they suffered from frostbite and bruising from the windscreen frame. The No 2 steward grasped the commander's right leg, which was stuck between the cockpit coaming and the control column whilst his left leg was wedged against his seat cushion. The steward then strapped himself into the left jump seat and was able to grasp both of the commander's legs but not before he had moved a further 6 to 8 inches out of the window frame. He held him by the ankles until after the aircraft had landed.
- The co-pilot had requested radar vectors to the nearest airport and had been turned towards Southampton Airport and eventually transferred to their approach frequency. Having verified that there was sufficient runway length available for a landing, the co-pilot manoeuvred the aircraft onto a visual final approach to runway 02 and completed a successful landing and stop on the runway at 0755 hrs. The engines were shutdown but the Auxiliary Power Unit, which the co-pilot had started up during the descent, was left running to provide electrical power to certain aircraft systems. As soon as the aircraft came to a halt, passengers were disembarked from the front and rear airstairs while the airport and local fire services recovered the commander back into the aircraft from his position half out of the windscreen frame, where he had remained throughout the descent and landing. He was taken to Southampton General Hospital suffering from bone fractures in his right arm and wrist, a broken left thumb, bruising, frostbite and shock. The other crew members and passengers were medically examined but apart from one steward who had cuts and bruising to his arm there were no other injuries.
Source: AAR 1/92, ¶1.1
The Windshield Replacement
- The BAC One-Eleven 500 series is a twin-engined, passenger aircraft powered by Rolls Royce Spey turbofans. The fuselage is pressurised and air-conditioned; 8,000 feet conditions being obtainable at 35,000 feet, under which conditions the pressure differential is 7.5 psi.
- The pilots' windscreens are of five-ply glass/polyvinyl-butyl construction, the innermost (glass) laminate being low-tempered to form a splinter shield in the event of a bird strike. Windscreen heating is applied, primarily to improve the impact resistance of the windscreen at low outside air temperatures. The windscreen is not designed on the 'plug' principal, where cabin pressure effectively contributes to holding it in place, but is fitted from the outside of the aircraft and is secured by means of 90 countersunk bolts, also fitted from the outside. The large number of bolts are required to prevent leakage of pressurised air through the window seal but the force of internal air pressure could be satisfactorily resisted by far fewer bolts.
Source: AAR 1/92, ¶1.6.3
- The windscreen was found near Cholsey, Oxfordshire, along with the windscreen outboard corner post fairing strip and some associated bolts.
- Of the 90 bolts used to attach the windscreen to the aircraft, 11 had remained in the windscreen and 18 were found loose nearby; one had remained in the aircraft window frame.
- Twenty-six of the bolts recovered with the windscreen were new bolts identified against the British Standard as having the part number A211-8C. The remaining four bolts recovered were re-used bolts identified as having the part number A211-7D. The illustrated Parts Catalogue (IPC) specifies that the attaching bolts should be part number A211-8D. The specifications for these bolts are:
- The bolts engage with 10 UNF Kaylock floating anchor nuts mounted on the inside of the windscreen frame. The replacement windscreen had been installed with 84 bolts (A211-8C) whose diameters were approximately 0.026 of an inch below the diameters of the specified bolts but of the same thread pitch, and six bolts (A211-7D) which were of the correct diameter, but 0.1 of an inch too short.
- The left windscreen had been changed during the night shift of the 8/9th June 1990 and the accident flight was the first since that installation. Eighty of the bolts which had attached the old windscreen were recovered from the work area during the investigation, and 78 of these were identified as A211-7D, the remaining two being A211-8D. The old windscreen, which had been fitted four years earlier, before the aircraft had been acquired by British Airways, had therefore been primarily attached by bolts which were 0.1 of an inch shorter than those specified.
Part No. | Shank length (inches) | Diameter (inches) | Thread Size |
A211-8D | 0.8 | 0.1865-0.1895 | 10 Unified Fine [UNF] |
A211-8C | 0.8 | 0.1605-0.1639 | 8 Unified Course [UNC] |
A211-7D | 0.7 | 0.1865-0.1895 | 10 Unified Fine [UNF] |
Source: AAR 1/92, ¶1.12.1
Of course this begs the question: how was the mechanic able to satisfactorily torque down screws with the wrong diameter and thread coarseness?
- During the course of the investigation British Airways carried out a simulation of the window fitting procedure to determine the torque that could be applied to 8 UNC countersunk head bolts fitting into 10 UNF Kaylock type anchor nuts.
- The combined results using 8 UNC bolts in 10 UNF Kaylock nuts showed a maximum torque of 12 lbf in and an average of 4.7 lbf in at thread slip.
- Examination of the torque limiting screwdriver used to fit the windscreen. Tests on a similar torque limiting screwdriver to that used to fit the windscreen showed that at a low setting (5 lbf in) the feel of the screwdriver clutch slipping was indistinguishable from the feel of an 8 UNC thread slipping in a 10 UNF anchor nut.
- The residual torque was confirmed as being high at a value of approximately 30 per cent of the torque set, rather than the usual value of between 5 and 10 per cent. Subsequent discussions with the manufacturer disclosed that the specification for the grease, used in the assembly of the torque limiting screwdriver, had been changed approximately five years ago because of problems of the grease breaking down with age. At this time retrospective action for those torque drivers already sold was considered impractical because of the large numbers involved and the lack of information about their location. The screwdriver under test was at least five years old and strip examination revealed that the excessive friction was caused by deterioration of the old specification grease. No significant wear was evident on the cam or the ball bearings, and when rebuilt with the correct grease the torque limiting screwdriver performed satisfactorily.
Source: AAR 1/92, ¶1.16
It is surprising that, given this knowledge, the entire set of torque screw drivers wasn't inspected because it was "impractical."
- Before the diameter of the replacement bolts had been established British Airways issued an instruction to be carried out on all its BAC One-Elevens before the next flight, to remove every fourth bolt from the No 1 left-hand and No 1 right-hand windscreens to check for correct length.
- Throughout the British Airways fleet of BAC One-Elevens two aircraft failed the check, having a total of 41 short bolts (A211-7Ds).
Source: AAR 1/92, ¶1.16
The report did not investigate the possibility that those aircraft windshields were also replaced by the same mechanic. Could the complacency behind these installations be isolated to one mechanic or is it more widespread? Indeed, could the previous installation of the accident aircraft also been the work of the same mechanic?
- A similar check was carried out on the four BAC One-Elevens belonging to another airline and two aircraft failed the check, having a total of 107 short bolts.
Source: AAR 1/92, ¶1.16
- The Shift Maintenance Manager glanced briefly at the Maintenance Manual as he had not changed a windscreen for about two years and wanted to refresh his memory. This check confirmed his impression that it was a straight forward job with no apparent difficulties.
- The IPC [Illustrated Parts Catalogue] was available on a microfiche reader, but was not used to identify the part number of the bolts to be replaced, consequently a stock check, using TIME [Total Inventory Management for Engineers], to assess the availability and location of replacement bolts was not carried out. The Shift Maintenance Manager justified this omission by saying that he was quite satisfied that the bolts that he had removed were the correct bolts, and that it would take so much time to find the correct numbers in the IPC that he did not feel justified in using the IPC in the circumstances of the job in question.
- The page of the IPC for the 528 series aircraft shows a sketch of the pilot's No 1 windscreen and the adjacent DV [Direct Vision] window, but only illustrates one bolt - that in the DV window, which is an A211-7D. The components for the pilot's No 1 window are listed in the text, along with several alternative modification states, and its bolts are defined as 'attaching parts' and are identified as A211-8Ds. The IPC for the 510 series, in contrast, is very clear in identifying the correct bolts.
- The bolts actually fitted to the defective windscreen were, in the main, A211-7Ds, the bolts illustrated as applicable to the DV window. That is bolts of the correct diameter but 0.1 of an inch shorter than those specified.
- The Shift Maintenance Manager removed the windscreen with the aid of the Avionics Supervisor, who also disconnected the electrical connectors of the screen heaters. The bolts were 'on condition' items, and as some of the paint-filled bolt heads had been damaged during removal, and others showed signs of corrosion, the Shift Maintenance Manager decided to replace them and took one of the bolts to the store to identify it by comparison with those held in the carousel. The carousels were under the control of a storeman and had drawers which were clearly labeled with a location code to which engineers were directed, after entering the part number into the adjacent stores computer terminal.
- Because of their small head size the bolts do not carry individual identification, but the Shift Maintenance Manager accurately matched the removed bolt by going through several trays, and comparing the removed bolt with the drawer contents. He then identified the part number of the bolt as A211-7D by looking at the stores issue note in the drawer (the windscreen should have been fitted using A211- 8Ds). The Stores Supervisor, who had been in the job for about 16 years, informed him that A211-8Ds were used to fit that windscreen, but did not press the point. The Shift Maintenance Manager decided that as A211-7D bolts had come out, he would replace them with bolts of the same size.
- The minimum stock level in the carousel for A211-7D bolts was 50, but there were only four or five bolts in the drawer (when checked by the AAIB the following Monday it contained four). The Shift Maintenance Manager drove to the unsupervised carousel underneath the International Pier, taking the removed bolt with him. The drawers in this carousel were labeled with the part number of the contents, although the labels were old and faded. The ambient illumination in this area was poor and the Shift Maintenance Manager had to interpose himself between the carousel and the light source to gain access to the relevant carousel drawers. He did not use the drawer labels, even though he now knew the part number of the removed bolt, but identified what he thought were identical bolts by placing the bolts together and comparing them. He also picked up six A211-9Ds, thinking that the attachment of the outboard comer post fairing strip would need longer bolts.
- The aircraft manual calls for a torque of 15 lbf in to be applied to the bolts, which are then retorqued to 5 lbf in after 100 flying hours. The Shift Maintenance Manager's experience told him that many of the bolts would be found up to three turns loose during the retorque procedure, so he decided to increase the initial torque to 20 lbf in.
- The British Airways toolstore at Birmingham held a calibrated dial indicating torque wrench to cover the range of 5 to 120 lbf in, but the retorque requirement of 5 lbf in was at the bottom of the range and the dial indicating torque wrench was not considered suitable for this task. Two calibrated torque checking gauges were available at Birmingham to allow engineers to confirm the wrench accuracy.
- The calibrated dial-indicating torque wrench was not available on the toolboard that night, but the Stores Supervisor had recently acquired from British Airways at London, on his own initiative, a torque limiting screwdriver specifically for the windscreen task, but on receipt it was found to be out of calibration date and it was therefore not cleared for use. It was not the company policy at Birmingham to allow the engineers to adjust torque wrenches as and when required, but rather to have the wrenches adjusted in a standards room and then issued for use at that specific setting. It was therefore the intention of the Stores Supervisor to have it set in the London standards room before issue, but, in the absence of any suitable alternative, the storeman set this screwdriver to the figure of 20 lbf in requested and gave it to the Shift Maintenance Manager, who checked the setting using both torque checking gauges.
- He fitted the windscreen using S4 of the bolts collected from the International Pier carousel and obtained a similar feel from the torque limiting screwdriver for each one; a feel that met his expectations. When he came to the outboard comer post fairing strip he realised that the A211-9D bolts were too long, descended from the staging and retrieved and refitted the six old bolts that he had removed with the fairing.
- The new bolts that he had fitted were in fact A211-8C bolts - one size down in diameter but with the same thread pitch as those specified and within 0.050 of an inch in length to the A211-7D bolts removed from the window. The bolts engage in 10 UNF 'Kaylock' floating anchor nuts; the self locking action is the result of part of the nut being an elliptical shape prior to the insertion of the bolt. Some of the anchor nuts were attached directly to the inside of the aircraft window frame and some were carried on strips, themselves attached to the window frame. The outboard corner post fairing strip interposed an additional thickness and required A2l1-8D bolts, and these were specified for the attachment of the whole windscreen, even though in the majority of locations approximately five threads would be visible below an anchor nut fastened directly to the frame when used with an A211-8D bolt. The amount of thread in safety would be reduced when used with the backing strips and the outboard comer post fairing.
Source: AAR 1/92, ¶1.17.4
The number of threads left over had been considered in the design of the window assembly; it is not up to the mechanic on scene to decide he or she knows better. If, for example, this mechanic had successfully installed the longer bolts for the corners, it could be that during pressurization the expansion of other components could interfere with these bolts. The "shade tree" mechanic on scene doesn't know and would be well advised to stick to the manual.
- The safety raiser used by the Shift Maintenance Manager did not give easy access across to the centreline of the aircraft, and he had to stretch over the aircraft nose to accomplish the task. Due to the inadequate access to the job and the obscuring effect of his left hand the Shift Maintenance Manager was not in a position to observe that the bolt thread was slipping in the anchor nut thread, instead of the torque limiting screwdriver allowing its shaft to remain stationary while the handle rotated. However, the bit and socket would have continued to rotate in his left hand.
- The window was finished in primer and had countersunk holes for the bolts; an A211-8C bolt head sits significantly further below the surface of the window, down in the countersink, than does an A211-7D bolt head, leaving an annulus of unfilled countersink which is easily discernable when viewed under good conditions. This 'excessive annulus' of unfilled counter sink was not seen
- When the bolts were being fitted to the windscreen centre column, the bolts from the right hand window, the heads of which filled the countersinks, were close to those of the left hand window, and, although painted, the difference is perceptible under normal circumstances. The Shift Maintenance Manager missed this difference in depth of the bolt heads in the windscreen centre column.
- When fitting the outside comer post fairing with the six bolts previously removed from it, the Shift Maintenance Manager failed to notice the difference in torque achieved or the difference in countersink: fit of the bolt heads between the old and new bolts.
- The following night the Shift Maintenance Manager carried out another windscreen change, this time a right hand one. The job had been set up before he arrived and he noticed that the bolts were A211-8Ds. He recalled fitting A211-7D bolts the previous night, but he rationalised that the aircraft were old and of differing modification states and the previous night he had an aircraft modification standard requiring A211-7D bolts and that night he had an aircraft requiring A211-8D bolts.
Source: AAR 1/92, ¶1.17.4
- The Shift Maintenance Managers did not criticise the shift system, however the potential problems associated with sleep deprivation and circadian effects were acknowledged and various strategies were cited to cope with the situation.
- During the initial part of the investigation the Shift Maintenance Manager who carried out the windscreen fit did not appear to grasp the lack of care that his actions implied. He co-operated fully in the investigation and, when shown the full list of errors and omissions that he had made, offered an explanation for each individual action.
- The person who fitted the windscreen was a Shift Maintenance Manager holding authorisations on BAC One-Eleven, Boeing 737, Boeing 757, HS 748 and with transit authorisations on L-1011 Tristar, Boeing 747 and a CAA licence holder for airframe and engines on the Viscount. His experience included 10 years in the RAF, followed by 23 years with British Airways. He appeared to be a mature, dedicated engineer who was well respected by flight crew and engineers alike.
- He had been on leave over the period of the last night shift carried out by his shift and so the Friday/Saturday night shift during which the windscreen was fitted was his first night work for approximately five weeks. He had had a normal nights sleep the previous night and had gone to bed at about 1730 hrs, and had slept for 1-1/2 hours, getting up at 2030 hrs. He said that he would have been happier if he had slept for an hour longer, but wasn't dismayed that he had not.
Source: AAR 1/92, ¶1.17
He had been in a "day cycle" for five weeks and for his first night shift he only had 1-1/2 hours sleep.
3
Analysis
- A number of procedures were ignored and some poor trade practices followed:
- The IPC, available to identify the required bolts' part number was not used
- The stores TIME system, available to identify the stock level and location of the required bolts, was not used
- Physical matching of old and new bolts by touch and eye was attempted, leading to a mismatch with bolts from the International Pier carousel
- Arbitrary choice of A211-9Ds to fit through the corner fairing took place
- An increase in bolt torque over that stated in the Maintenance Manual was used.
- Non conformity with British Airways standards was also demonstrated: An uncontrolled torque limiting screwdriver was set up outside the Calibration Room.
- During the course of his duties the Shift Maintenance Manager reviewed the work of his shift, this review augmented the self certification task required of the engineers by British Airways' maintenance policy. Once he had decided to carry out rectification work himself, he withdrew from the active supervision of the rest of the shift. The task of the windscreen installation was not designated a 'Vital Point' and consequently no duplicate inspection was called for and none took place, nor was the work of the Shift Maintenance Manager subject to review by another manager.
- Thus the Shift Maintenance Manager had no backstop with any chance of detecting his errors. Errors that were made more likely by the sleep deprivation and circadian effects associated with the end of a first night shift.
- The adoption of self certification systems within manufacturing industry has typically resulted in savings, mainly arising through reduction in scrap and in the achievement of higher manufacturing efficiency. Nevertheless, at the end of the production line the product is normally still tested, before being despatched. Some aircraft maintenance tasks which may be undertaken using self certification procedures do not allow for the testing of the end product before it is flown.
- Many of the actions taken that night by the Shift Maintenance Manager may be described as evidence of a lack of sufficient care in the execution of his responsibilities. Such a catalogue of events does not equate to a momentary lapse in behaviour but is more indicative of the approach of a conscientious and pragmatic engineer working in an non-procedural manner. Such a description of the individual is not necessarily inconsistent with his 'exemplary record', because until matched with a task such as this windscreen change, his approach was capable of going undetected by anything other than a close observation of his workpractices.
Source: AAR 1/92, ¶2.2
I would characterize the mechanic's actions as one of someone who thinks he is smarter than the people who designed the airplane and doesn't need to adhere to strict procedure as a result. He assumes that matching the new bolts to the old is good enough. He believes a longer bolt is needed for the corners but is unconcerned when he discovers the bolts he used are shorter than those for the next windshield change. He dismisses the advice of the parts supplier who says another bolt is called for. He decides is own torque procedure (20 lbf instead of 15 lbf) is better than the manual's.
- The number of errors perpetrated on the night of this job came about because procedures were abused, 'short-cuts' employed and mandatory instructions ignored. Even when doubt existed about the correct size of bolt to use, the authoritative documents were not consulted. After the event the Shift Maintenance Manager concerned demonstrated a lack of appreciation of the significance of failure to adhere to the specified procedures, good trade practices and even the requirements of the Maintenance Manual.
- There is clear evidence of a different philosophy applied to pilots, who are required to undergo regular line and base standardisation checks, and engineers who are not subjected to any comparable standardisation or refresher checks.
Source: AAR 1/92, ¶2.2
4
Cause
- A safety critical task, not identified as a 'Vital Point', was undertaken by one individual who also carried total responsibility for the quality achieved and the installation was not tested until the aircraft was airborne on a passenger carrying flight.
- The Shift Maintenance Manager's potential to achieve quality in the windscreen fitting process was eroded by his inadequate care, poor trade practices, failure to adhere to company standards and use of unsuitable equipment, which were judged symptomatic of a longer term failure by him to observe the promulgated procedures.
- The British Airways local management, Product Samples and Quality Audits had not detected the existence of inadequate standards employed by the Shift Maintenance Manager because they did not monitor directly the working practices o f Shift Maintenance Managers.
Source: AAR 1/92, ¶3 (b)
References
(Source material)
Aircraft Accident Report 1/92, Report on the accident to BAC One-Eleven, G-BJRT over Didcot, Oxfordshire on 10 June 1990, Air Accidents Investigation Branch, Department of Transport, London, February 1992.