One of the problems with small operators is the lack of functional check flight expertise. This problem can be exacerbated by aircraft manufacturers unwilling to share test procedures (also known as test schedules) for fear of liability problems. That is a recipe for a mishap, even with careful pilots who may not have considered every angle of an assigned task.
— James Albright
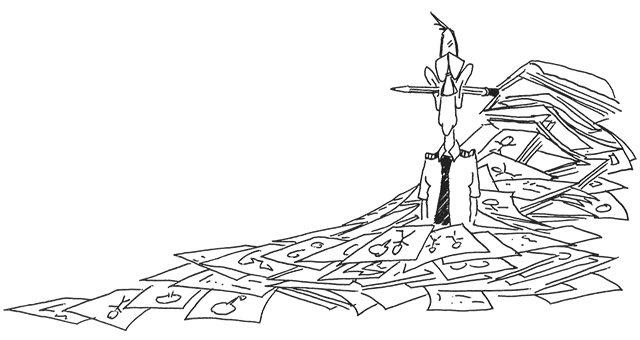
Updated:
2017-01-01
This crew was assigned the task of checking out a wheel brake that was causing the aircraft to pull to one side. They were concerned with keeping the aircraft on the runway during high speed tests but did not consider brake energy limits. They failed to consult brake energy charts and to consider the fact brake temperatures tend to rise for about 30 minutes after brake application. They exceeded brake energy limits by a wide margin. A design flaw in the airplane allowed hydraulic fluid to feed a brake fire, heavily damaging the airplane.
Before undertaking a functional check flight crews have a lot of work to do and may need to consider the possibility they are unqualified for the assigned duty. More about this: Functional Check Flights.
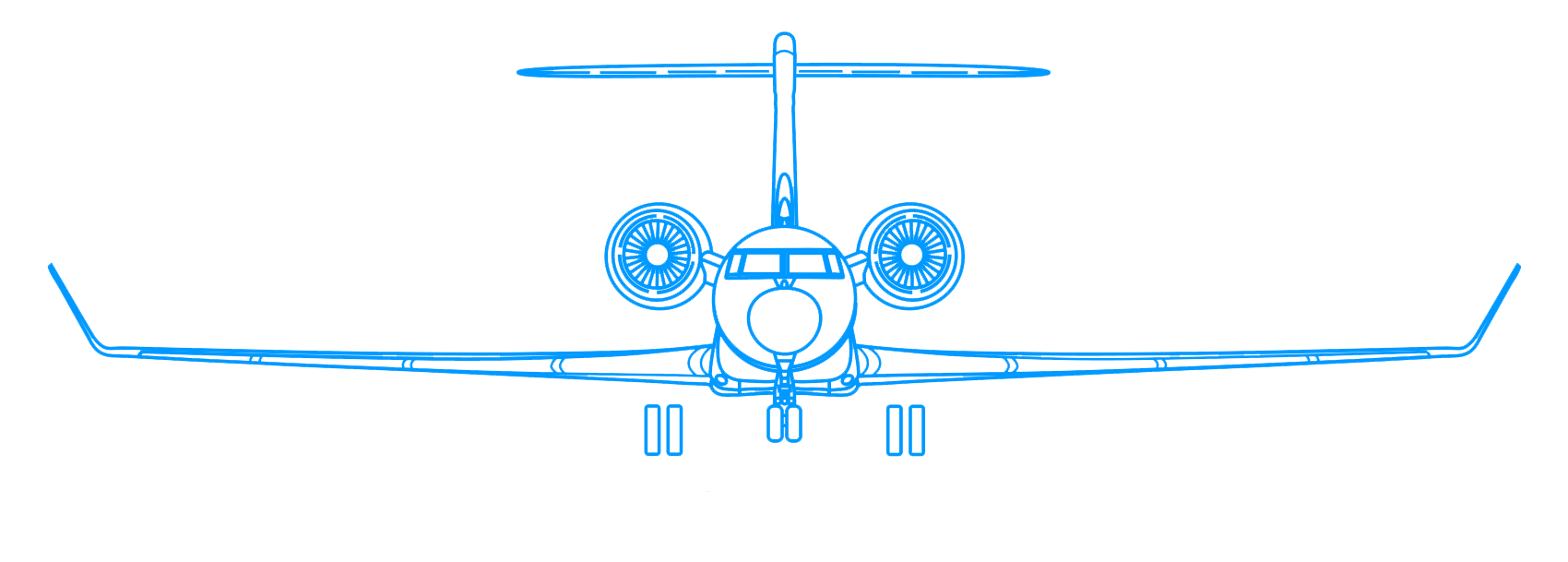
1
Accident report
- Date: 11 November 2009
- Time: 1259
- Type: Falcon 2000
- Registration: CS-DFE
- Fatalities: 0 of 3 crew, 0 of 3 passengers
- Aircraft Fate: Fire damage to tires, fuselage, landing gear, and wing.
- Phase: Ground
- Airports: (Departure) Biggin Hill, Kent (BQH/EGKB), United Kingdom; (Destination) Biggin Hill, Kent (BQH/EGKB), United Kingdom
2
Narrative
- In the evening 10 November 2009, the commander received a text message from the operator notifying her to be at Biggin Hill Airport at 1130 hrs for a “miscellaneous activity” to include “high-speed taxi requested by maintenance department”. The intended activity was not designated as an Operational Check Flight (OCF) or Test Flight (TF), which have specific meanings and requirements.
- On arrival at the maintenance organisation, the maintenance team were with the aircraft on the parking area ready for the test. The flight crew were briefed that the aircraft was reported as pulling to the left when the toe brakes were applied. The maintenance team had carried out low speed taxi tests and another flight crew had conducted tests up to 50 kt, as a result of which the left brake units had been changed with the right brake units to see if the problem still occurred. The maintenance team requested high-speed tests, which the crew agreed to but advised they would adopt an incremental approach starting at 50 kt and increasing to 80 kt.
- The crew carried out performance calculations to ensure the runway length was adequate for the task to be performed. The main runway at Biggin Hill is orientated 03/21 and is 5910 ft long by 147 ft wide and has a tarmac surface which was dry. They estimated that the balance field length required for an abandoned takeoff at V1 for the weight and ambient conditions was 3,000 ft. The crew decided that it would be possible to carry out two low-speed runs, one after the other, in the full runway length available.
- The crew commenced a series of accelerate/stop runs along the runway by selecting takeoff thrust, accelerating to the target IAS, then retarding the thrust levers and applying the brakes positively, bringing the aircraft to a stop. The first two runs were up to 50 kt IAS using Runway 21 before turning around and performing two 60 kt runs along Runway 03. The aircraft cleared the runway at holding point A3, in order to allow another aircraft to depart, and then taxied back to the threshold of Runway 21. The aircraft was cleared to enter Runway 21 to commence the next taxi test at 1248 hrs. The aircraft was accelerated to 80 kt and the commander had to apply full left brake in order to keep the aircraft straight. A second run was carried out to 50 kt and this was normal in maintaining runway alignment, but as with the other runs, the anti-skid system was activating at the lower speeds.
- The aircraft was turned around and another 80 kt run was carried out along Runway 03, but this time the aircraft veered to the left. The maintenance supervisor on the jump seat and the flight crew discussed the findings and it was agreed to carry out one more run along Runway 21. The aircraft was taxied to the end of Runway 03 and turned around onto Runway 21 in order to perform another 80 kt test. The commander accelerated the aircraft, but before 30 kt, the test was abandoned as the crew believed they had a flat tyre on the left Main Landing Gear (MLG). They informed ATC and requested a tug, but shortly after, the pilot of another aircraft holding at D2 informed ATC that there was a fire on the left MLG of CS-DFE. ATC confirmed this visually and at 1257 hrs advised CS-DFE that there was a fire and to evacuate the aircraft. The crew carried out the evacuation drills and all those on board left the aircraft without difficulty through the normal airstair door. The Airport Fire and Rescue Service (AFRS) responded immediately and extinguished the fire.
Source: AAIB CS-DFE, pg. 16
3
Analysis
- Both the left MLG brake units and the number three brake unit from the right MLG were removed and sent for disassembly and inspection at the manufacturer’s overhaul facilities.
- The inspection found that all three units displayed severe heat damage after experiencing ‘exceptionally’ high brake energies. The elastomeric static and dynamic piston seals were completely destroyed (seal degradation would have started at a temperature of 183°C). The aluminium alloy housings within the brake piston assembly had melted, indicating temperatures in excess of 200°C and the pistons themselves were significantly deformed (Figure 5). The protective coating on the carbon discs had been removed indicating temperatures in excess of 1,200°C.
- Using the recorded flight data, the manufacturer assessed that each of the left brakes had absorbed just under 18 MJ of energy and each of the right brakes just over 11 MJ2 from the cumulative effect of eight braked runs conducted during the incident.3 During certification the brakes had been tested up to 15 MJ on the aircraft and 16.4 MJ during brake qualification tests. Based on the data obtained from development testing with a fully worn heat sink, 16 MJ of brake energy was assessed to elevate the brake temperature by approximately 1,600°C.
Source: AAIB CS-DFE, pg. 23
Reason for test flight: operators manual vs. aircraft manual
- The operator’s Operations Manual (OM) Part A, contains the relevant information with regards to TFs. . . A test flight must be performed after special maintenance and/or repair work on an aeroplane and on special request of the authority.
- The Approved Maintenance Manual (AMM) for the Falcon 2000 does not specify taxi trials to be conducted as part of any defect troubleshooting activity. There is no test schedule published by the manufacturer in any of the aircraft manuals for conducting the kind of braking tests attempted by the operator.
Source: AAIB CS-DFE, pg. 25
Flight crew's risk analysis
- The crew were properly licensed and qualified to operate the aircraft. Whilst the commander had met the 500 hours on type minimum requirement for OCFs, she had not carried out the training to conduct an OCF and was not included as such on the I Jet system. The high-speed taxi trials had not been identified as an OCF and no test schedule was available.
- Following the briefing by the maintenance supervisor, the flight crew carried out a risk assessment of the test activity. They considered the greatest hazard was overrunning the end of the runway whilst carrying out the accelerate/stop manoeuvre. This was addressed by carrying out the appropriate performance calculations. By incrementally increasing the target speed for stopping the aircraft they also addressed the possibility of significant lateral departure from the runway centreline. However, the risks associated with exceeding the brake energy limit were not identified by the crew or the maintenance team.
Source: AAIB CS-DFE, pg. 25
4
Cause
No probable cause was explicitly listed, though several recommendations were made from which causes can be inferred.
- Whilst attempting to troubleshoot a braking defect, the crew conducted eight high speed rejected takeoffs, within a 15 minute period, with limited distance travelled at taxiing speeds and no significant periods of cooling between runs. The cumulative effect of this was to subject the left gear brake units to energy levels in excess of what they were designed to accommodate and the certified limits demonstrated during aircraft development. This raised the temperature of the brake components to the point where the hydraulic fluid seals failed and significant structural damage occurred. Consequently, hydraulic fluid was released at high pressure which rapidly ignited on the hot brake surfaces, resulting in a sustained fire around the left MLG.
- The leak was caused by operation of the aircraft beyond its approved limits, which is an issue that cannot necessarily be mitigated by the manufacturer.
- Whilst the crew had been shown the brake energy graphs and calculations during their type conversions, they had not used them since. The brake energy limit is rarely encountered during normal aircraft operation, which may have reinforced an understanding by both pilots that brake energy was not a concern under any circumstances and they did not recognise the cumulative effect of carrying out multiple accelerate/ stop manoeuvres.
- A ‘flight-test’ schedule would have provided structure to the activity and an opportunity for a more formal risk assessment to be conducted. This would have addressed the runway overrun and lateral runway departure issues as well as the brake energy implications. Whilst the crew might have consulted the brake energy information in the flight manual, the manufacturer emphasised that the information derived was not appropriate for the purposes of this test activity.
Source: AAIB CS-DFE, pg. 31
References
(Source material)
Air Accidents Investigation Branch, Incident, Falcon 2000, CS-DFE, 12/2010.