Having started my big airplane career with a cockpit crew of four, then three (lost the navigator), and then two (lost the flight engineer), I must admit to being a bit agnostic about the debate for going back to three pilots on the flight deck. On the one hand, it is another person to worry about. On the other hand, when things go wrong, having a third pilot up front can be a life saver. Take the example of United Airlines Flight 1175.
— James Albright
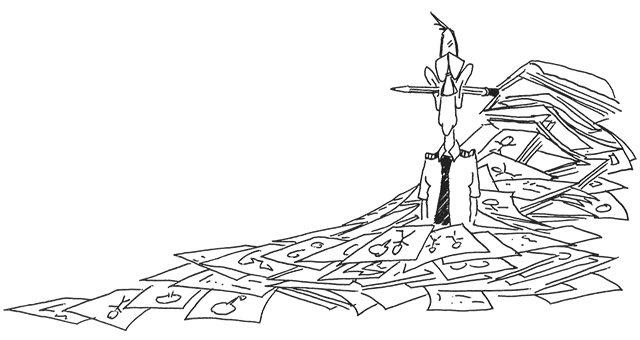
Updated:
2024-12-01
These three pilots appeared to have done everything right and if any of the three were not present, the outcome would have been doubtful. This incident also points out that as pilots, we are at the mercy of so many other people. In this case, somebody made the decision that the people doing fan blade inspections didn't need the training previously considered to be the minimum. So we pilots sometimes end up with an airplane that doesn't perform as intended. Finally, this incident points out that all the training we get in simulators cannot cover every possible situation. The more experience you have, the better. But more than that, the more deeply you know your airplane and think about these things, the higher your odds for survival. (And that's a good thing for your passengers too.)
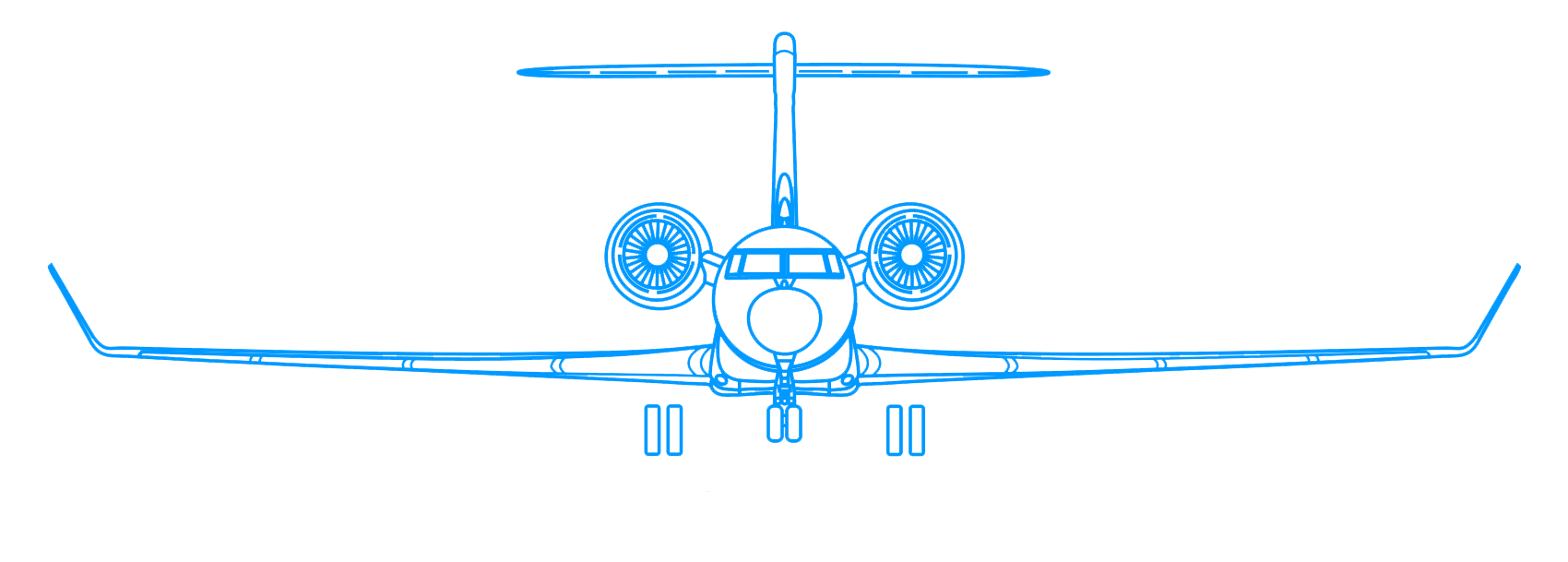
1
Accident report
- Date: Feb 13, 2018
- Time: 1302
- Type: Boeing 777-222
- Operator: United Airlines
- Registration: N773UA
- Fatalities: 0 of 378 persons*
- Aircraft Fate: Damaged
- Phase: En Route
- Airport: (Departure) San Francisco International Airport (KSFO), California, USA
- Airport: (Destination) Honolulu International Airport (PHNL), Hawaii, USA
* The NTSB report says 378, interviews with the Captain report 381.
2
Narrative
The sterile report
The final report downplays pilot actions, as if this engine failure was just like any other.
On February 13, 2018, about 1200 Hawaiian standard time (HST), United Airlines flight 1175, a Boeing 777-222, N773UA, experienced an in-flight separation of a fan blade as well as portions of the inlet and fan cowl of the No. 2 (right) engine, a Pratt & Whitney (P&W) PW4077, over the Pacific Ocean enroute to the Daniel K. Inoyue International Airport (HNL), Honolulu, Hawaii. While the airplane was in level cruise flight at flight level (FL) 360, the flight crew heard a loud bang that was followed by a violent shaking of the airplane followed by warnings of a compressor stall. The flight crew shut down the engine, declared an emergency, and proceeded to HNL without further incident. There were no injuries to the 374 passengers and crew onboard and the airplane received minor damage. The flight was operating under the provisions of 14 Code of Federal Regulations Part 121 as a regularly scheduled passenger flight from the San Francisco International Airport, San Francisco, California (SFO) to HNL.
At the time of the event, there were three pilots on the flight deck: the captain, who was the pilot monitoring, the first officer (FO), who was the pilot flying, and a jump seat rider, who was an off-duty United Airlines 777 FO.
The flight departed SFO on time and the push back, taxi, takeoff, and climb were normal. The flight was about 120 miles from HNL at flight level (FL) 360 when there was a violent jolt and very loud bang that both pilots stated was followed by extreme airframe vibrations. The pilots reported that immediately after the jolt and loud bang, the autopilot disconnected, and the airplane began to roll to the right. A positive exchange of controls was accomplished with the captain becoming pilot flying. The pilots stated that about 15 to 30 seconds after the jolt and loud bang, the engine instruments indicated a failure of the number 2 engine. After accomplishing the Severe Engine Damage checklist, the crew shut down and secured the engine. The jump seat rider stated that after the right engine was shutdown, the vibration subsided although the controllability of the airplane was not normal. The crew declared an emergency and began a drift down descent to FL 230. The captain directed the jump seat rider to go back into the cabin to assess the condition of the engine. The jump seat rider noted that the engine was oscillating and that the cowling was missing. He took a video of the engine to show the captain and the FO what they were dealing with. The pilots reported that concurrently, the purser had come to the flight deck and the captain briefed her about the emergency and that they would be landing at HNL. The airplane continued to HNL and made a visual approach and landed on Runway 8R without further incident.
Source: NTSB, p. 3
The pilots
The pilots were very experienced. The report mentions a third off duty pilot who was a qualified 777 FO, but doesn't give any further details.
The captain, age 57, reported a total of 13,592 hours total time, with 360 hours in the B777. He held an FAA Airline Transport Pilot certificate with type ratings in the B777, B747, B737, B757, B767, and SD-3. He held a valid first class medical certificate with a restriction for glasses for near vision. His most recent flight review was October 10, 2017.
The first officer, age 60, reported a total of 11,318 hours total time, with 10,087 in the B777. He held an FAA Airline Transport Pilot certificate with type ratings in the B777 and B747. He held a valid first class medical certificate with a restriction for glasses for near vision. His most recent flight review was October 3, 2017.
Source: NTSB, p. 4
In an interview with the captain, we learn the jump seat pilot had just finished his initial training as a Boeing 777 first officer.
The engines
The PW4077 engines are central to this incident, specifically the fan blade inspection process.
The PW4077 is a dual-spool, axial-flow, high bypass turbofan engine that features a 1-stage 112-inch diameter fan, 6-stage low pressure compressor (LPC), 11-stage high pressure compressor (HPC), annular combustor, 2-stage high pressure turbine (HPT) that drives the HPC, and a 7-stage low pressure turbine (LPT) that drives the fan and LPC.
The PW4000 112-inch engine fan blade is a hollow core, wide chord airfoil made of a titanium alloy with 6 percent vanadium and 4 percent aluminum as alloying elements. The fan blade is about 40.5-inches long from the base of the blade root to the tip of the airfoil and about 12.5- and 22.25-inches wide at the blade root and blade tip, respectively. A fan blade weighs a maximum of 34.85 pounds.
Source: NTSB, p. 5
3
Analysis
The fan blade failure and resulting damage
The Number 11 blade had a crack in it that should have been picked up at its last two inspections, but the inspectors were not properly trained. That blade broke off during flight and took out a neighboring blade. At least one of these blades penetrated the engine cowl forward of the Kevlar shield, causing much of the forward cowl to be lost. The subsequent drag caused the engine vibrations and the aircraft's loss of altitude beyond what would be expected in drift down calculations.
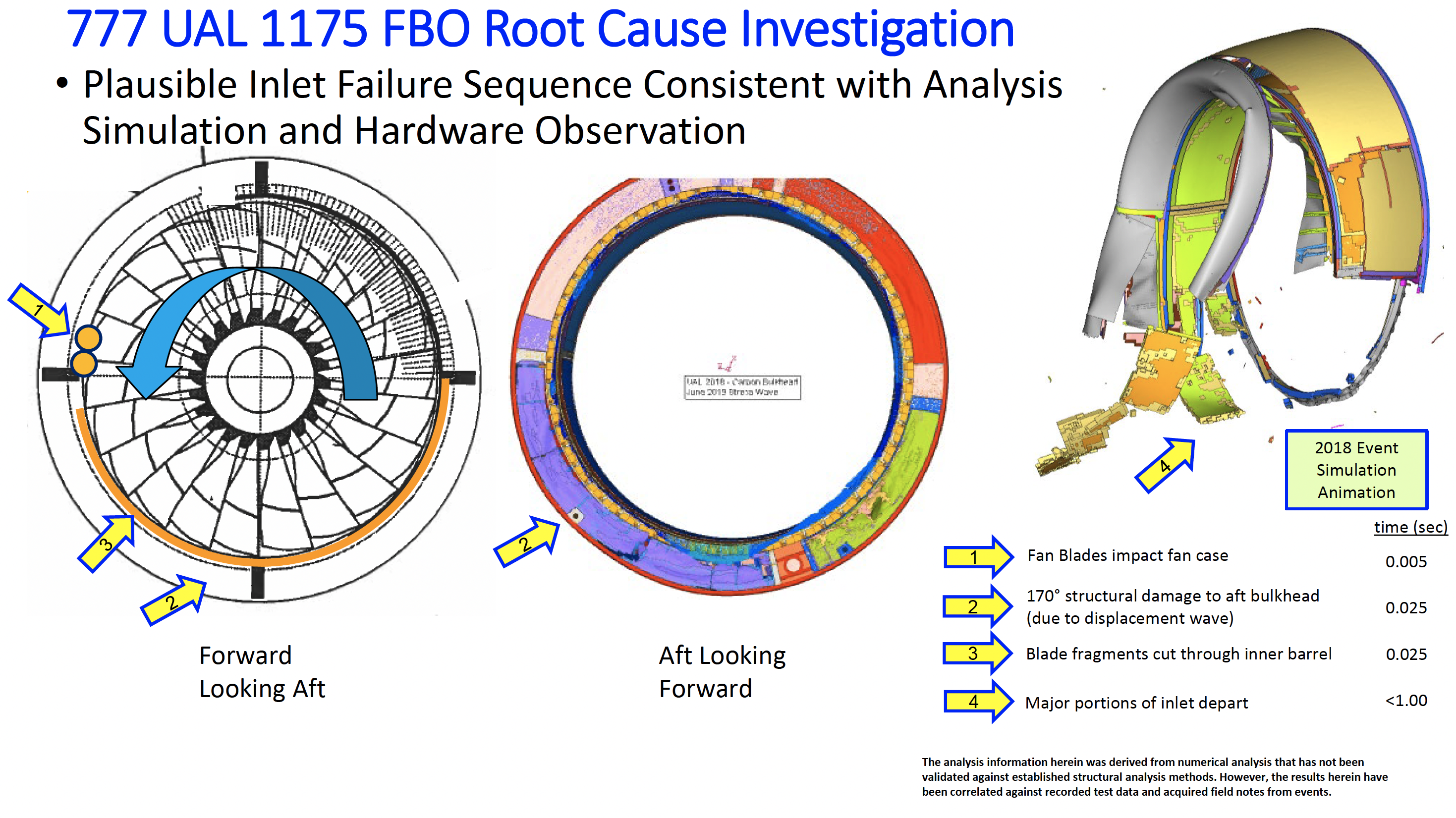
Fan blade root cause, Boeing Overview
The fan blade in position No. 11 was fractured transversely across the airfoil about 1.44-inches above the fairing at the leading edge and slightly below the surface of the fairing at the trailing edge. There was a piece of fan blade found up against the leading edges of the fan exit guide vanes at about 4 o'clock. This piece of fan blade was about 15-inches wide chord wise, 23-inches long radially, and had a fracture surface on the inner end that corresponded to the fracture surface on blade No. 11.
Metallurgical examination revealed a fatigue fracture that had initiated from a subsurface origin in a region of micro texturing consisting mostly of primary alpha crystals on the interior surface of the hollow core fan blade. The examination also revealed that the fan blade's material conformed to the specified titanium alloy's requirements.
There was extensive damage to the interior surface of the fan case in the form of gouging and cracking. Although there were cracks in the case and the outer layer of the Kevlar wrap was split, there was no penetration of debris. The Kevlar® environmental wrap was in place around the fan case. The Kevlar environmental wrap had an approximately 35-inch long axial tear at about 3 o'clock that was between about 5.5- and 40.4-inches aft of A-flange. The outermost layer of the Kevlar under the environmental wrap was visible through the tear and there was an area that was approximately 3-inch axial by 2-inch circumferential about 15-inches aft of A-flange that had a frayed appearance and there were tears and separations. The Kevlar environmental wrap had a wrinkled appearance between about 1 and 5 o'clock with outward bulging of the belt between about 2 and 4 o'clock. The maximum deformation of the Kevlar environmental wrap was about 2.5-inches at about 3 o'clock. The location of the maximum deformation of the wrap was coincident with the approximately 34-inch long crack on the inside of the fan case.
The majority of the inlet assembly was missing. All the inlet lip skin, the forward bulkhead, most of the inner and outer barrels, and about half of the rear bulkhead were not recovered. The majority of both inner and outer halves on the fan cowl were also missing. The missing parts were lost at sea.
Source: NTSB, pp. 7 - 8
The fan blade inspection process
United Airlines utilized P&W, the engine manufacturer, to accomplish inspection and overhaul of the fan blades per maintenance manual requirements. The installed set of fan blades, including the fractured fan blade, had undergone two overhauls at which time the blades underwent a thermal acoustic imaging (TAI) inspection. At the initial TAI accomplished on the fractured fan blade in 2010, there was a small indication at the location of the origin of the crack. Review of the records from the 2015 TAI show that there was a larger indication in the same area.
The TAI inspection process is used to detect internal and external cracking in hollow core fan blades. Sound energy is utilized to generate an excitation of the fan blade's internal and external structure. The sound energy excitation will cause relative movement between each side of a contacting discontinuity that will cause frictional heating. The frictional heat generated by the movement of each side of the discontinuity is detected on the surface of the fan blade by a thermal sensor. After both sides of the fan blade have been completely scanned, the images are processed by a computer that are then displayed on a monitor for the inspector to evaluate. The computer has the capability to enhance the image to assist the inspector in evaluating any indications. Certain types of indications may require the inspector to reinspect the area, which may require repainting of the fan blade and repeating the TAI process. If a fan blade has an indication that the inspector is not able to clearly evaluate, the inspector is to forward the images along with the fan blade to a Process Engineer for further evaluation and possibly further nondestructive testing such as ultrasonic and/or x-ray inspection.
P&W initiated the TAI inspection process around 2005. From the outset of the inspection to the time the United Airlines fractured fan blade was inspected and up to the time of the incident at HNL, P&W did not have a defined training and certification regimen for the TAI inspectors. The 1st shift inspector was trained by the engineers who developed the process and the 2nd shift inspector, who was the one who last inspected the United Airlines fan blade that fractured, was trained by the 1st shift inspector. Both inspectors stated that their training on the TAI was about 40 hours of on-the-job training. In comparison, the certification requirements for the commonly used eddy current and ultrasonic inspections are 40 hours of classroom training and 1,200 and 1,600 hours of practical experience, respectively. In 2005, when the TAI was initiated, P&W, following standard NDT industry practice, categorized the TAI as a new and emerging technology that permitted the inspection to be accomplished without establishing a formal training program and certification requirements. In 2015, when the fractured fan blade was last inspected, and in 2018, when the fan blade fractured, P&W still categorized the TAI as a new and emerging technology, although over 9,000 fan blades had been manufactured and inspected. P&W did offer training on the TAI, however, the 1st and 2nd shift inspectors were not permitted to attend so that they could work on clearing the backlog of fan blades that were in the shop. After the incident, P&W reported that they had developed a curriculum for TAI initial and recurrent training.
The TAI is accomplished in an enclosed air-conditioned room within P&W's overhaul and repair facility in East Hartford, Connecticut. The room has large windows that allow the afternoon summer sun to shine into the room. The TAI thermal scanners can detect the incremental temperature increase that occurs if there is a defect in the blade and the afternoon sun would cause ghost images on the thermal scans. Although the inside of the TAI room is air conditioned, the shop area is not air conditioned so the workers in the area would often go into the room to cool off in the summer. The TAI scanners would capture the thermal image of the worker. The TAI room air conditioner could not keep the room to within the required temperature limits for TAI in the summertime and they had to place an additional portable A/C unit in the room. After the incident, P&W put screens up and tinted the windows as well as installing flashing lights to alert the shop workers that a TAI is ongoing to preclude the false thermal images. In addition, P&W upgraded the room's air conditioner that can maintain the temperature to the TAI's requirements.
Source: NTSB, pp. 8 - 9
I believe the highlighted text is the root of the cause. If we ever find out who at Pratt & Whitney made the decision to forgo the training, we will know who almost cost the lives of 378 people, if not for the skill of the pilots.
Pilot statements
The following are taken from the Captain (CA), First Officer (FO), and Jump Seat (JS) pilots. Everything is sourced from "Statement for NTSB" as submitted by each. I've blended them for readability and to highlight what happened.
[FO] At approximately 120 NM from Honolulu, we were at FL360, autopilot and auto throttles engaged. There was a violent jolt followed by extreme vibration and high noise level. The autopilot disengaged so I grabbed the controls to fly the aircraft and silence the EICAS Warning for Autopilot Disconnect. The aircraft was rolling right.
[CA] I put my hand on the control and told him, “I have the aircraft.” There was a positive change of control; I became pilot flying and First officer became pilot monitoring.
[FO] I looked to the EICAS and engine instruments to analyze what was happening. It seemed like a delay of 15-30 seconds (I may have experienced temporal distortion) and noted the right oil quantity at zero and announced “Severe Engine Damage Right” and recommended I run that unannunciated checklist.
[CA] We immediately accomplished Severe Engine Damage checklist, followed by Drift Down Procedure checklist. I asked [JS] to declare an emergency with [Honolulu Center] and then we contacted dispatch and advised them of the incident and requested that they contact NOC, Maintenance, and Honolulu Operation.
[FO] We secured the engine IAW the checklist. The vibration reduced somewhat but the controllability was still not normal. I ran the Driftdown checklist. We started a descent to FL230 at 231 KTS. The TAC (Thrust Asymmetry Compensator) was off so I ran the reset checklist but it wouldn’t reset.
[CA] We decided the most suitable airport in time, distance, and familiarity was Honolulu International Airport. We requested that they notify the airport and have the equipment standing by upon our arrival. I then asked [JS] to go back and evaluate the condition of the engine while he was back there the Chief Purser had come to the cockpit and I briefed her on what was going on (that we had lost right engine and we were making an emergency landing into Honolulu International Airport).
[JS] Due to continued airframe vibrations, I was sent aft to evaluate the status of the right engine, right wing, & empennage. At the same time, the lead FA came to the flight deck to brief with [CA]. I reported that the right engine was oscillating and the cowling was missing; with no apparent damage to the wing or noticeable fluid leaks but there were rumbling noises & vibrations in the aft galley area. Additionally, I took a live picture and video clip of the right engine with my work iPad to show CA and FO what we were dealing with.
[CA] The aircraft continued to Honolulu and we made a single engine approach to runway 8R and landed safely. Aircraft was met by the Fire Marshal and escorted to the gate where the remaining engine was shut down and the aircraft was secured without further incident.
4
Cause
The National Transportation Safety Board determines the probable cause(s) of this incident to be: the fracture of a fan blade due to P&W's continued classification of the TAI inspection process as a new and emerging technology that permitted them to continue accomplishing the inspection without having to develop a formal, defined initial and recurrent training program or an inspector certification program. The lack of training resulted in the inspector making an incorrect evaluation of an indication that resulted in a blade with a crack being returned to service where it eventually fractured.
Source: NTSB, p. 2
5
Postscript
Captain Chris Behnam has become a bit of a celebrity and you can find him giving speeches or being interviewed. A good source for these kinds of stories is the Blancolirio YouTube Channel, where host Juan Brown interviewed Captain Behnam: YouTube blancolirio, Capt. Behnam UAL 1175 Fan Blade Out Event Interview. Captain Behnam details what happened. Here is a synopsis of what he said.
[ . . . ] I went to the bathroom, came back, put on my seatbelt and turned around to talk to [the FO] to start doing the briefing for the approach when [ . . . ] there was a huge explosion followed by tremendous vibration and deceleration. We literally hit the glareshield, the impact was so severe [ . . . ] and the autopilot disconnected and she rolled to about 45 degrees of bank at 36,000 feet, Mach 83, without any warning [ . . . ] I went into what I am trained to do, take care of the airplane, first fly it, and as I applied left aileron, my foot went in for left rudder, and before I knew it, I had full left deflection on the aileron and rudder, and she stopped at 45 degrees of bank, hesitated, and I asked [the FO] to help me push the nose over to break the angle of attack so she came back and throughout this confusions [ . . . ] I asked the other guys, what's going on? Both engine instruments were normal.
As the NTSB report showed, both engines looked normal for about 30 seconds, because the damage took out the Electronic Engine Control wiring. After 30 seconds, the right engine indications went away.
As soon as I saw the problem and noticed this, I said, we have a severe engine damage, let's run the checklist. But the cockpit was shaking so violently and the noise was so loud [ . . .] the [FO] tried to read the [Electronic Checklist] he tried to reach it and couldn't put his finger on it. So we did it the old fashioned way, autothrottle off, throttle back to idle, and it was all verified, and right engine shut down, from memory. After we shut the engine down, the vibration didn't stop. [ . . . ] The [JS] said pull the fire handle [ . . ] pull the fire handle and things went more towards normal. [ . . . ] This is not your normal engine failure, there is something serious wrong here. [ . . . ] This took every ounce of my energy and concentration to fly the airplane, she didn't want to fly, she just was not flyable, the wing was compromised. It made it very difficult.
Juan Brown notes that the diameter of a Boeing 777's engine is about the size of the Boeing 737's fuselage. The absence of the front cowl is creating a huge amount of drag on the right side of the airplane, and making the aircraft so hard to control.
I had already lowered the nose because my left eye was looking at the airspeed [ . . . ] it was coming back and you know [ . . . ] you're not going to maintain 36,000 feet on one engine and I know it's going to be around mid-20's. [ . . . ] I had my left hand on the yoke, my right hand on the throttle, I had fire walled the left engine because I saw the airspeed coming back but I'm already lowering the nose and I knew I have 200 miles to go [ . . . ] we have a big problem here. I have to baby this thing for almost 200 miles, 40 minutes to Honolulu.[ . . . ] I asked for drift down and [FO] told me that 23,000 feet and 240 knots. So as I am slowing to 240, at 242, 243, she starts buffeting again. [ . . . ] At 265 knots, she felt like she was going to fall apart.
A windmilling dead engine is usually better than a seized dead engine because it offers less drag. But in this case the windmilling engine didn't have a cowl to direct the air flow, hence the vibration. The drift down speed table was no longer viable, since the stall speed had become higher with all that drag on one wing.
They entered the clouds at 33,000 feet and never broke out until 2,000 feet.
[ . . . ] the deck was about 2,000 feet. [ . . . ] Runway 8 Left was closed that day, 4 Right was too short for the condition, having an engine out, hydraulics out, and all that, so only runway available for us was 8 Right, but it doesn't have an ILS. So we had to shoot an RNAV approach IMC into 8 Right. [ . . . ] I delegated the communications with ATD and the flight attendants to [JS], so he declared the emergency with [Honolulu Center] while I'm flying the airplane, and initially [FO] and I wanted to work on the checklist, but it was just too much. So it literally became a three-man cockpit. [ . . . ] I asked [JS] to work with [FO] on the checklists for one person and I said I'm just going to focus on the instruments and keep the blue side up and fly towards Honolulu and you guys deal with ATC and the flight attendants and run the checklist. [ . . . ] Every seven or eight minutes, I would turn around and tell the guys to forget what just happened, let's focus going forward because you know we as pilots, on a check ride [you think you made a mistake, just put it behind you.]
They still didn't know why they aircraft was so difficult to control.
About 15 minutes into this incident, I asked [JS] to go back there [because] the vibration and shaking was still there and the noise level was really high. So I asked [JS] to go back there with his iPad and video whatever it was that was going on, so we had a visual. That's when he came back with that [video]. Once I saw that, I knew what we were dealing with.
Juan Brown asked about being able to maintain altitude.
[ . . . ] in my mind created the CDAP, three to one, constant descent angle approach, just coming in and doing a curve, a right turn on an arc to Runway 28 Right, because we knew that we only had one shot at this and having max thrust just to maintain 1200 feet per minute clean, we all believe that once we dirty up the airplane she's not going to be able to go around.
United crews normally get their aircraft performance numbers from ACARS, but that was inoperative. The JS used his iPad application to figure it out. They numbers said they needed 7,960' of runway, which was available on Runway 8R.
So I told the guys I'm gonna come in high and fast because altitude and airspeed are my friend. Altitude to a certain point, but once you get on glideslope you got to lose the altitude. But speed is always your friend so we came at 250 knots about 12 DME. I brought the power back slightly put the flaps to one, we got the green light so there was a big sigh of relief.
They had planned for a no flap landing, just in case.
And the next thing was get the gear down, so we put the gear down and we got the green lights. [ . . . ] I was doing about 220 knots with the gear down, a thousand feet we put flaps five and came down the three degree glide, by that time we were visual. But I was on instruments. The guys were giving me vectors, turn left five, turn right five, stop turn. [ . . . ] just like the old PAR [ . . . ] they said, you just stay on the instruments and we'll get you down there. [ . . . ] we came down at flaps five at 200 knots. At 200 feet, we went flaps 20, and I held 180 till touchdown. I knew the numbers were compromised [ . . . ] and I told [JS] to do the "Brace, brace, brace," but it happened to be a very smooth landing.
References
(Source material)
YouTube blancolirio, Capt. Behnam UAL 1175 Fan Blade Out Event Interview
Boeing "Overview of Failure Sequences and Root Cause Statements," in NTSB Docket, DCA18IA092
National Transportation Safety Board (NTSB) Aviation Incident Final Report, DCA19IA092, Boeing 777-222, February 13, 2018.
National Transportation Safety Board (NTSB) Powerplants Group Chairman's Factual Report, DCA19IA092, Boeing 777-222, February 13, 2018.