Have you ever wondered how a typical aircraft engine hydraulic pump works? Me too. It isn't your typical pump with one piston going up and down or one or two gears which mesh in a way to push fluid. Hydraulic pumps tend to be axial piston pumps. You won't find much about them in aircraft manuals because this is "assumed knowledge" among designers or it is stuff deemed unnecessary for us to know.
— James Albright
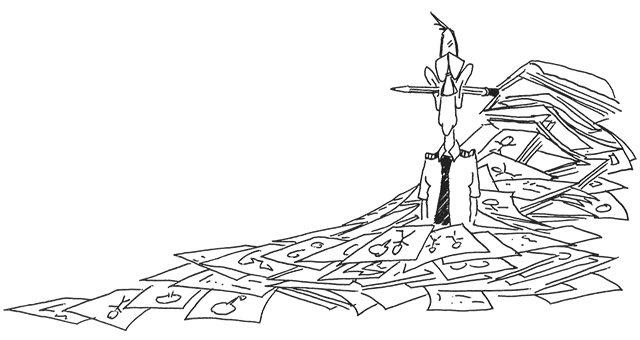
Updated:
2021-02-18
I think knowing how the pump works helps us to understand how it is we can get constant pressure and variable volume out of these pumps.
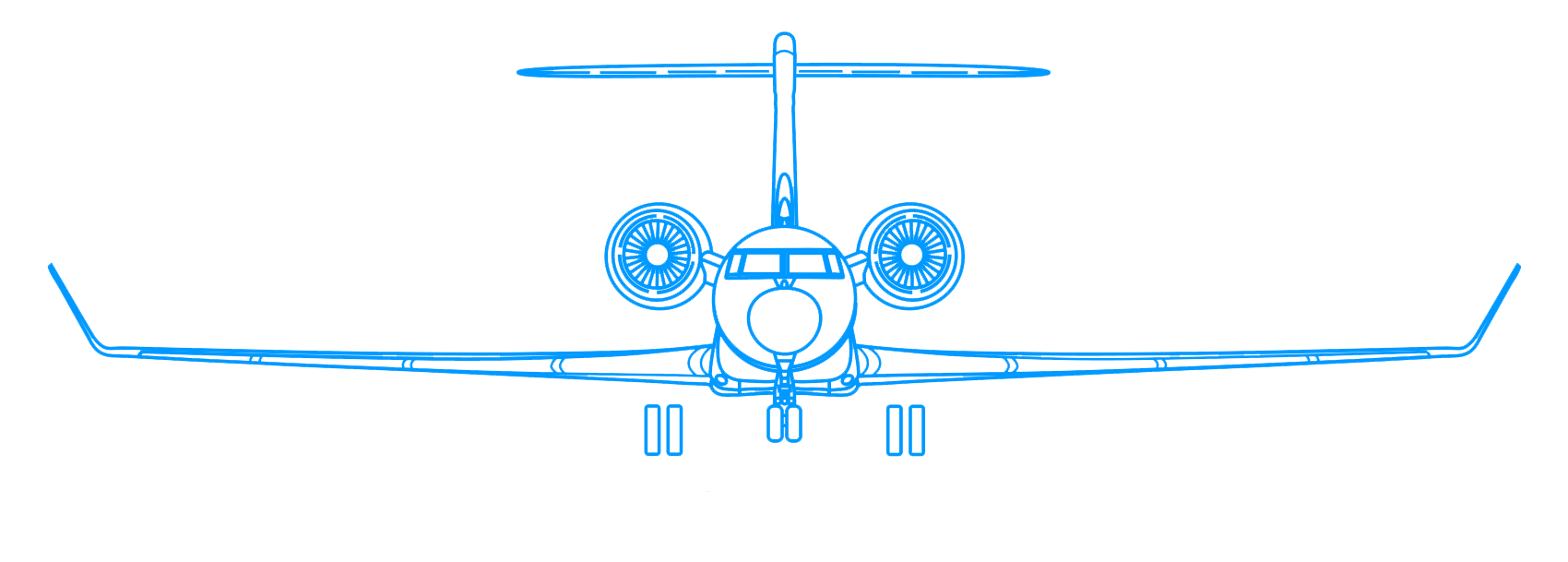
An axial piston pump has a number of pistons arranged in a circle within a housing which is commonly referred to as a cylinder block or barrel. This cylinder block is driven to rotate about its axis by an integral shaft that is usually aligned with the pumping pistons (usually parallel but not necessarily).
The pumping pistons protrude from the opposite end of the cylinder block. There are numerous configurations used for the exposed ends of the pistons but in all cases they bear against a cam. In variable displacement units, a tilted disk, commonly called a swashplate, provides the cam action needed that leads to piston reciprocation and thus pumping. Variable displacement units have the ability to vary the angle of the swashplate during operation whereas fixed displacement units do not.
In a variable displacement pump, if swash plate is set parallel to the axis of rotation, there is no movement of the pistons in their cylinders. Thus there is no output. Movement of the swash plate controls pump output from zero to maximum.
In a typical pressure-compensated pump, the swash plate angle is adjusted through the action of a valve which uses pressure feedback so that the instantaneous pump output flow is exactly enough to maintain a designated pressure.
I think this is how constant pressure and variable volume happens:
Let's say engine speed goes up, therefore the rate of rotation of the pump goes up. That, of course, increases the volume produced in any given unit of time. If we connect a pressure sensor that decreases the swashplate angle when the pressure tries to increase, we'll return to the desired pressure even while producing greater volume.
If, on the other hand, engine speed decreases, the volume produced per unit of time will decrease. That same pressure sensor can be used to increase the swashplate angle when the pressure tries to decrease and we return to the desired pressre even though the pump is producing less volume.